Industrial Ergonomics
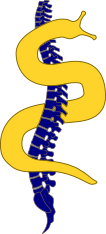
The application of ergonomic principles to the workplace in order to reduce the risk of musculoskeletal disorders (MSDs). MSDs are injuries to the muscles, tendons, ligaments, nerves and supporting tissues. MSDs are typically caused by repetitive motion, forceful exertion, awkward postures, and vibration.
Programs
- Exoskeleton Program – Some of the most strenuous activities in the workplace include lifting and transporting heavy objects. The exoskeleton’s functions support the body and help prevent musculoskeletal disorders and increase safety. As a result, they contribute to reduced time loss and improving occupational safety.
- Industrial Athlete Program – Similar to sports athletes, Industrial Athletes are individuals who perform work duties and services with high physical demand. Industrial athletes lift, bend, push, and move in identical ways that a typical sports athlete would, sometimes for longer durations and higher frequency. This makes the industrial athlete just as vulnerable to physical and in some cases, psychosocial injury. The program is designed on 4 fundamentals of sports medicine: Prevention, Early Intervention, Acclimatization, and Knowledge. The goal of the program is to equipped the worker with the skillset to proactively prevent injury.
Services Provided
- Ergonomic risk assessments – Identifying and assessing the risk of musculoskeletal disorders (MSDs) associated with a specific job or task.
- Ergonomics and biomechanics training – Educating employees on how to use their bodies safely and efficiently.
- Work hardening – Assist employees to prepare their bodies for the physical demands of their specific job duties.
- Injury prevention programs – Train employees on proper body mechanics, nutrition, conditioning, and awareness.
- Ergonomic interventions – Making changes to the workplace or the way work is done to reduce ergonomic risks. This could involve changes to equipment, work processes or job design.
If you have further questions or need consultation on any industrial ergonomic safety concerns, please contact ergocruz@ucsc.edu.